Making It In India
Tyromer's entry to the Indian market comes at a time when the Indian government has set ambitious targets for both India-based manufacturing and scrap tire management.
In July 2022, the Indian government implemented legislation that would have the country recycle 100% of all end-of-life tires by 2025. Given that 100m scrap tires are produced annually in the country, this goal is ambitious indeed—and Tyromer is pleased to announce that we will officially play a role in helping to meet it.
Partnership with Apollo Tyres
At the 2022 International Rubber Conference in Bangalore, India, Tyromer and Apollo Tyres announced a sustainable materials partnership. Apollo’s Chief Advisor for R&D, PK Mohammed, said in a statement:
“This partnership with Tyromer is a step towards achieving our sustainability goals… Producing new tyres using sustainable raw materials is currently the most efficient path to meet our circular economy goals.”
Meanwhile, Tyromer’s CEO Sam Visaisouk said, “We are thankful to the Apollo Tyres’ team for its support of our vision of direct tire-to-tire recycling.”
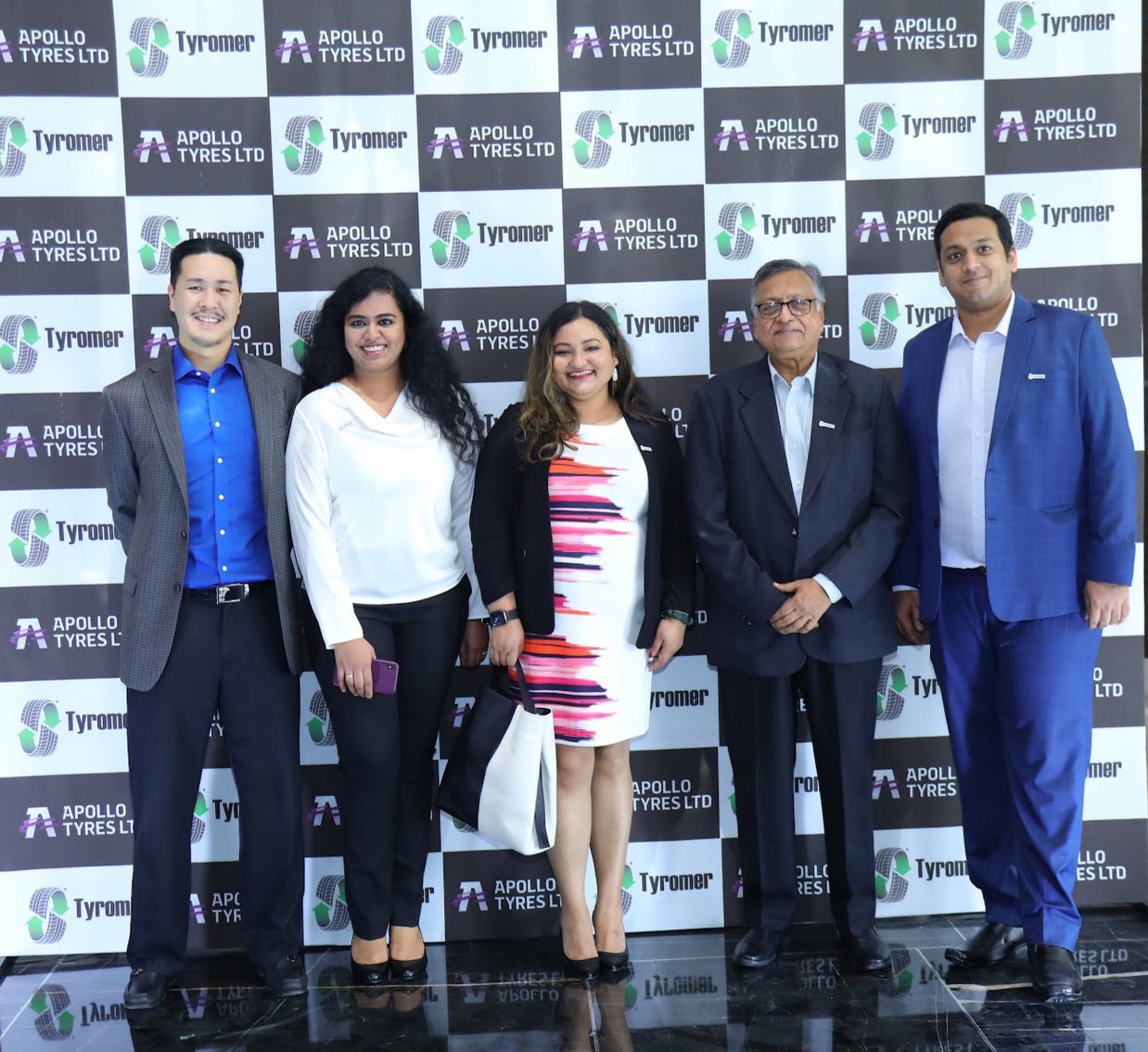
Tyromer India LLP, which will spearhead our Indian operations, is run by BK Jalan and Adarsh Jalan. As our COO Jon Visaisouk says, they’re “incredible partners who connect at all the right levels.” Based in Chennai, Tyromer India will begin with one manufacturing line producing 8000 metric tonnes of TDP annually. The Chennai plant is large enough that it can be expanded to accommodate four Tyromer devulcanisation lines, with a potential total production capacity of more than 30 000 metric tonnes per annum.
Innovation in the Indian tire industry
The Indian tire industry has already shown its willingness to adopt innovative and sustainable practices. Apollo, for example, has set the goal of becoming carbon neutral by 2050. Steps towards this goal include improving water management, transitioning 25% of power consumption to renewable energy by 2026, and using 40% of sustainable materials in tire compounds by 2040.
Apollo’s decision to use Tyromer’s tire-derived polymer, or TDP, in their tires will reduce carbon emissions and consume less energy compared to virgin materials. According to Apollo’s PK Mohammed, Tyromer’s TDP will also help the company as they strive to meet extended producer responsibility (EPR) laws. These laws, which are gaining popularity around the world, require manufacturers to take responsibility for the final waste product. Newly-introduced EPR tire laws in India stagger recycling targets. For 2022-23, producers must recycle 35% of tires; the following year the increment increases to 70%; and by 2024 all end-of-life tires must be recycled.
In November 2022, Apollo and Tyromer discussed the possibility of setting up scrap tire collection points by leveraging Apollo’s dealer network. Currently, the collection of scrap tires on a large scale is not efficiently organised in the country; Apollo’s efforts here may thus serve as both an inspiration and example for other companies. Generally speaking, EPR laws will likely have a positive impact across the entire industry, as they create incentives to find new, high-value solutions.
Hopes for the future
For many years, India imported scrap tires from countries such as the UK, Malta, and Australia; processing, however, did not keep pace with imports. The dumping of scrap tires is also a problem around the country. Projects like the tire park at IIT Kanpur help to highlight the need for action, but as they are essentially art installations they do not continuously reduce the number of scrap tires. Further compounding the problem is a lack of licensed recycling operations that can process such volumes of tires in a environmentally safe manner. In 2019, the New Indian Express reported that “as per the Telangana State Pollution Control Board’s own admission, all 61 [licensed pyrolysis operations in the state] are non-compliant to various environmental norms.” Meanwhile, Reuters reported that “there is also a vast trade to backyard pyrolysis operations” that do not abide by environmental regulations.
Tyromer’s devulcanisation process uses no added chemicals—in fact no additives at all. As such, we hope to reduce the number of scrap tires in India while at the same time contributing in a positive way to the environment and local economy. We also hope that our technology can make up part of the shortfall of domestic natural rubber production.
As of 2019, India produced just over 50% of the rubber that it consumed. Yet high import duties on natural rubber have hamstrung Indian tire manufacturers and in 2021, the Automotive Tyre Manufacturers Association (ATMA) cited these costs as “a major deterrent for the tyre industry to support domestic manufacturing.” ATMA also observed that “lower availability of natural rubber…disrupts the production processes at tire manufacturing units even as the demand for tires is peaking.”
Tyromer’s tire-derived polymer provides a robust, stable source of local rubber. In addition to supporting India-based manufacturing, TDP can also shield companies from market volatility at a time when climate change puts natural rubber harvests at risk—especially since many rubber-producing areas are susceptible to increased severe weather events like droughts and typhoons. Geopolitical developments may also make imports more volatile in the future. For these reasons, it is of utmost importance for the Indian tire and automotive industry to establish alternative and reliable sources of rubber.
We look forward to introducing our technology to a wider audience, working towards its inclusion in more tires and other applications, and making the circular economy a reality in the global tire industry.